Some 11+ years ago, I started messing with servos and PIC microcontrollers as switch machines. Originally it was just for Ron Renner’s Wind River in Denver, where we didn’t want to spend the money to upgrade all the twin coil machines to Circuitron Tortoises. In an afternoon, I had a primitive workable design, and Ron’s layout eventually got dozens of them installed. Each was hand-built and installed in place using double-sided foam tape for both the servo and the PCB.
Those early prototypes then went on to become the basis for Iowa Scaled Engineering’s MRServo line a couple years later. The MRServo matured over the years, moving to surface mount components and then proper 3D-printed mounting brackets to make installation more reliable. But fundamentally, the design remained little changed from the earliest units.
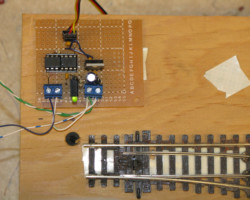
We (Iowa Scaled Engineering) discontinued MRServo about three years ago because sales had tapered off, more large players had entered the market (Walthers) and we never got any sizable market share away from the dominant vendor, Tam Valley. There was nothing about our offering that was fundamentally compelling and differentiating from the others. Plus they were a pain to build and support for relatively little profit margin.
The MRServo Version 4
That’s not to say MRServo died, though. It just went from being a product back to a project. My layout still uses them exclusively as switch machines, with probably close to 100 installed. They’re great for me because they’re relatively inexpensive (especially if I’m building them myself), they’re low profile (so they fit up inside the benchwork without issue), and they take a logic level input to control them (so they’re easily run by the signal system). A few months back I got the itching to again improve the design. I wanted to improve the input protection structure, which often got static-zapped, and also move to an AVR so that I could make changes in C rather than PIC assembly. When I designed the original servo controllers, I was still using PICs regularly and programming in their assembly variant. However, having gone to AVRs and GCC around the same time, I haven’t used a PIC in a new design since.
One other minor change is that I’ve started putting 2-piece terminal blocks on the boards. That makes it significantly easier to connect wires under the layout, as I can pull out the connector, screw in all the wires, and then just plug it back in.
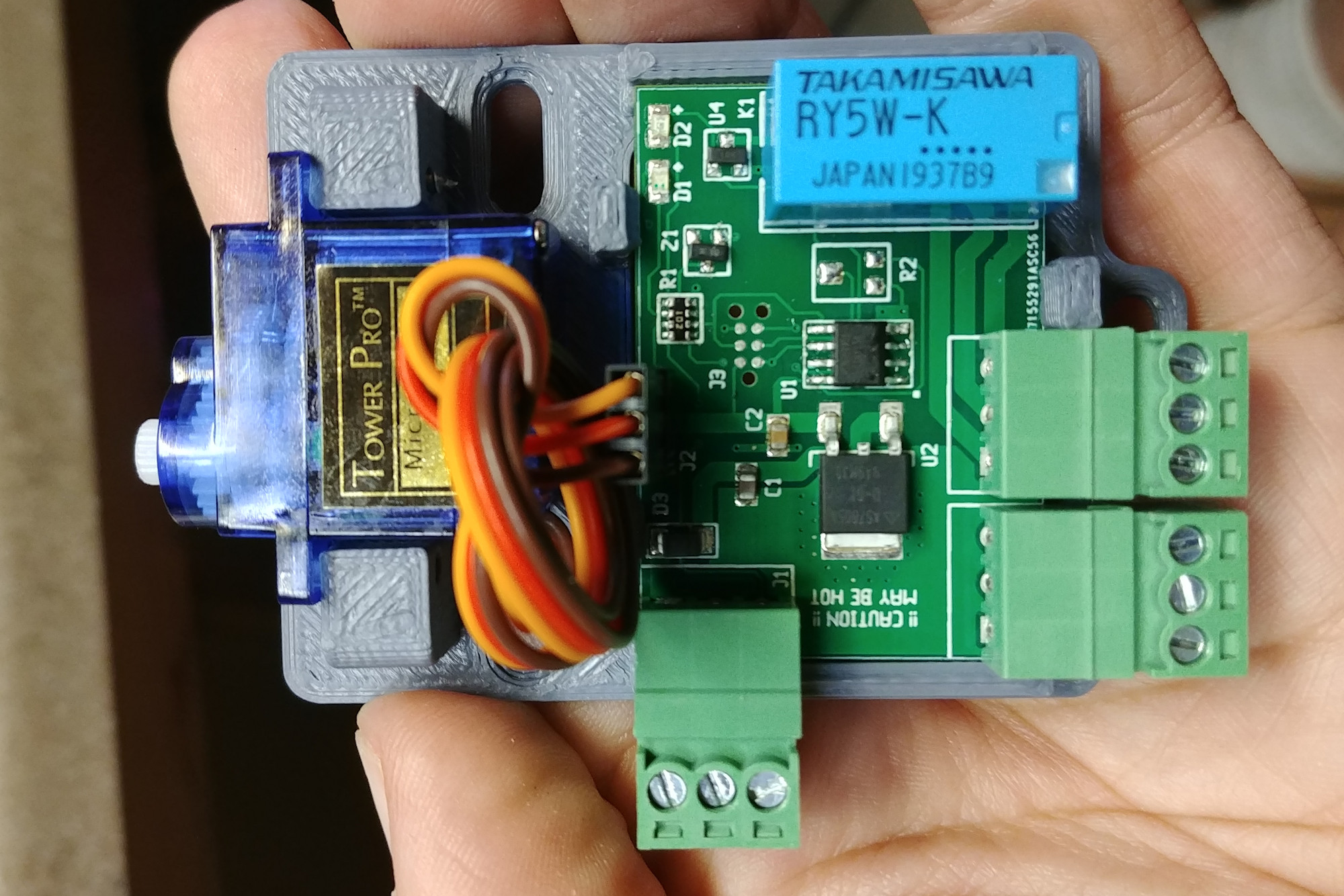
Like all of its predecessors, the MRServo v4 is open hardware. The source code and design files are all available on Github.
Just wanted to say, I really appreciate seeing the update post and hearing that the MRServo is still alive and kicking in one form. I picked up about 10 of them for my small layout many, many years ago. Mine are MRServo-1’s. I 3D printed a ton of the brackets (had a 3D printer at work that was being de-accessioned and had a lot of filament to burn through) in the hopes of purchasing more. A few years ago I decided that I’d try upgrading my MRServo-1’s to -3’s. Went through old websites, photos and diagrams to figure out what components to buy (I’m not super technical when it comes to this stuff!) which I did, but have yet to test out the upgrade. (I’ve never done through-hole soldering.) Anyway, I enjoyed reading the backstory and the update. Hoping to continue to see more on this and maybe one day I’ll have the courage to dive in. In case this is the same person, I was the guy who came up to the IASE table at Springfield this past winter to inquire about the MRServo’s. 🙂 Thanks!